Alabaster Carving: Achieving Translucence and Detail
There's a quiet magic to alabaster. It’s a stone that feels ancient, whispering stories of the earth’s deep time. Holding a piece of raw alabaster in your hands evokes a sense of connection to something profoundly older than ourselves, a tangible link to the patient processes of geological formation. When skillfully carved, alabaster possesses a breathtaking translucence, a soft inner glow that can transform a simple form into a luminous work of art. It’s a craft demanding patience, precision, and a deep respect for the material’s inherent qualities – a pursuit that draws parallels, I find, with the meticulous restoration of antique accordions; both are testaments to enduring beauty and the enduring power of human craftsmanship.
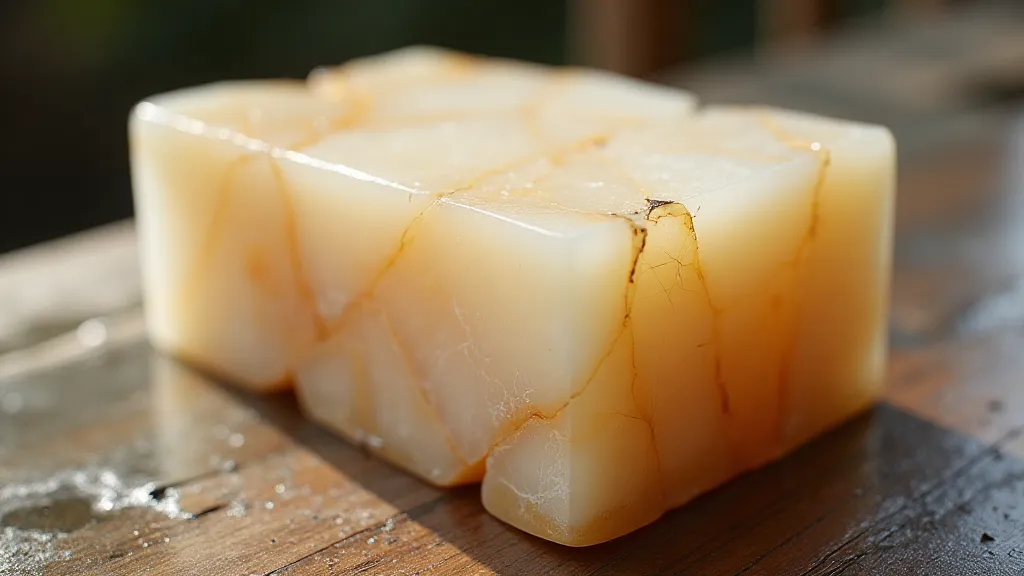
A Stone Steeped in History
The history of alabaster carving stretches back millennia. Ancient Egyptians used it for small statues and vessels, while the Romans prized it for decorative elements in their homes and temples. In Europe, particularly in Florence, Italy, alabaster carving flourished from the Middle Ages through the Renaissance, producing intricate religious figures and architectural details. The town of Volterra, in Tuscany, remains a significant center for alabaster production today, carrying on a tradition passed down through generations. It's humbling to consider that the stone you might be shaping today has, in some form, been handled by artisans across centuries, each adding their skill and dedication to its ongoing story.
My own interest in alabaster carving began, unexpectedly, with a fascination for antique accordions. These instruments, often made with delicate bellows, intricate carvings, and aged ivory keys, possess a similar quiet elegance and require a similar degree of reverence in their preservation. Both alabaster and the aged wood of an accordion have absorbed the atmosphere of their time – the touch of countless hands, the echoes of music and prayer. The care required to bring an accordion back to life – cleaning, repairing, replacing missing parts – mirrors the careful shaping and polishing of alabaster, aiming to reveal the beauty that lies beneath the surface.
Understanding Alabaster’s Qualities
Not all alabaster is created equal. The stone varies significantly in its composition, color, and translucence. The degree of translucency is primarily determined by the size and distribution of the mineral grains within the stone. Fewer, smaller grains allow more light to pass through, resulting in a more luminous appearance. Colors range from creamy white to yellow, brown, green, and even pink, influenced by trace elements present during formation. Choosing the right piece of alabaster is the first crucial step in any carving project.
It's essential to assess the stone’s internal structure. Look for fractures and inclusions – these can weaken the stone and make carving more difficult. A piece of alabaster that feels slightly warm to the touch is often a good sign; it indicates a higher degree of translucency. The grain structure also matters; finer-grained alabaster is generally easier to carve and yields more detailed results. The challenges presented by different stone types often necessitates a well-equipped workspace. For those new to stone carving, exploring introduction to stone carving – a beginner's guide – is a great starting point. Understanding the basics of various carving methods can dramatically improve your results and help avoid common pitfalls.
Carving Techniques for Translucence
Achieving translucence in alabaster carving isn’t just about selecting the right stone; it's about employing specific carving techniques. The key is to avoid aggressive removal of material that can disrupt the stone’s internal structure and scatter light. A slow and deliberate approach is paramount.
Initial Shaping: Begin with rough shaping using a bolster and mallet. This removes the bulk of the excess material, but be mindful of the stone's grain. Working with the grain, rather than against it, prevents chipping and breakage. A coping saw can be useful for cutting intricate shapes.
Detailing: Smaller tools, such as carving knives and rifflers, are used for detailing. These tools allow you to refine the form and create subtle curves and planes that enhance the stone’s luminosity. The angle of the tool is crucial; holding it at a slight angle helps to create a beveled edge that catches and reflects light.
Sanding: Sanding is an integral part of the process. Begin with a relatively coarse grit (around 120-grit) and gradually work your way up to finer grits (up to 1000-grit or higher). Wet sanding is generally preferred, as it helps to lubricate the stone and prevent clogging of the sandpaper. Each pass of the sandpaper removes a thin layer of material, smoothing the surface and increasing the stone’s translucence. Patience is key – rushing this step can result in a dull, lifeless finish. Proper care and cleaning are also vital for preserving the beauty of your finished piece. For those interested in mastering relief carving techniques – a popular and rewarding option – resources like basic relief carving guides offer valuable insight into creating stunning three-dimensional artwork from alabaster.
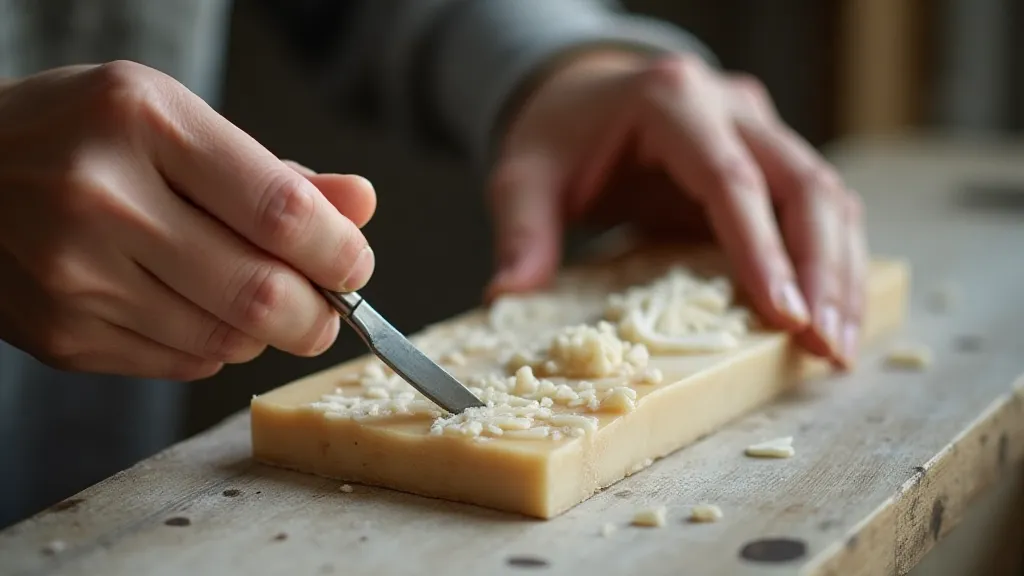
Highlighting Detail: A Delicate Balance
While translucence is a desirable quality, achieving intricate detail is equally important. The two aren’t mutually exclusive; in fact, they complement each other. The play of light and shadow across a highly detailed surface enhances the perception of translucence. To achieve this, focus on creating subtle variations in depth and plane.
Consider the angle of the light source. The direction from which the light enters the stone will influence how the detail appears. Experiment with different lighting conditions to see how the carving looks in different environments. Small, carefully placed details – a delicate fold in a garment, a subtle curve of a lip – can bring a carving to life. The selection of the right stone is only the beginning; understanding the nuances of different stone types is essential for achieving exceptional results. For instance, when working with other sedimentary stones, the techniques will vary significantly. Those looking for a contrast to alabaster may find inspiration in exploring carving with limestone and learning how to work with its unique texture and grain. Limestone, with its softer nature, presents a different set of challenges and opportunities for the artisan.
Beyond Alabaster: Exploring Sedimentary Stones
The principles discussed here largely apply to other sedimentary stones as well, although their specific qualities and best-suited techniques will differ. For example, working with travertine will demand a different approach to sanding and polishing to account for its porous structure. Similarly, the grain direction and density will significantly impact carving ease and the final aesthetic. Expanding your skill set beyond alabaster unlocks a world of creative possibilities and allows you to tailor your craft to the unique properties of each stone.
The Enduring Appeal: A Link to the Past
Alabaster carving is more than just a craft; it's a connection to the past. It’s a way to engage with the earth's history and to appreciate the skill and dedication of artisans who came before us. The meticulous restoration of antique accordions, like the careful shaping of alabaster, speaks to a reverence for craftsmanship and a desire to preserve beauty for future generations. Whether you are a seasoned carver or a novice just beginning to explore the possibilities of this remarkable stone, the journey of creation is its own reward. The gentle glow emanating from a finished piece of alabaster is a testament to the enduring power of art and the quiet magic that lies within the earth. Remember that safety is paramount when working with any material, and understanding the potential hazards is key to a successful and enjoyable carving experience. Consider reviewing safety first: stone carving safety guidelines for best practices and preventative measures. It's crucial to wear appropriate personal protective equipment, and to understand the proper handling and disposal of carving dust.
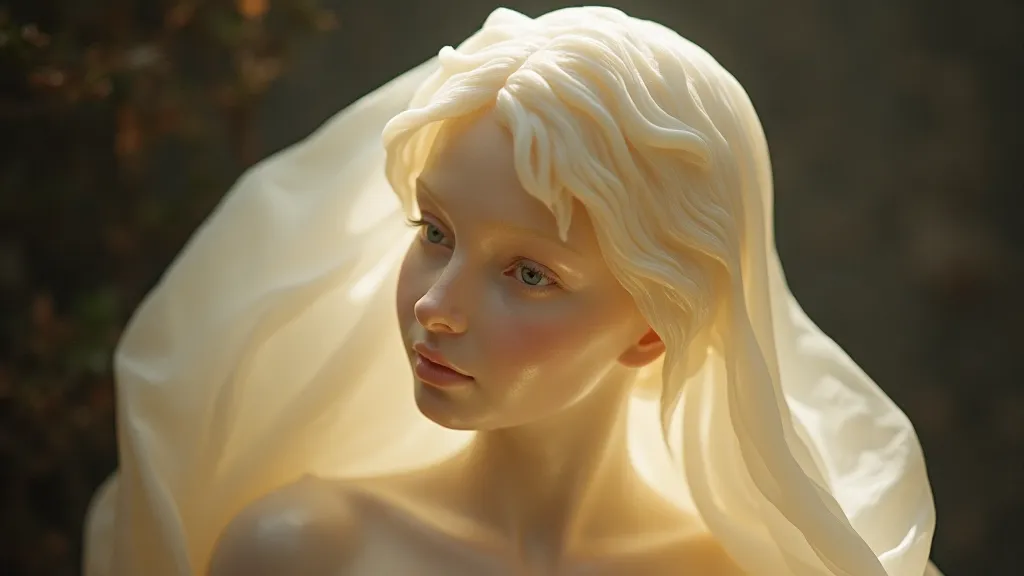